Oil-Immersed Transformer Problems & Solutions – Expert Prevention Guide
Discover top oil-immersed transformer failures (leaks, overheating, insulation issues) and proven prevention methods. Boost reliability with 2024 maintenance tips!
1. Insulation System Failures (45% of Cases)
Key Problems:
- Transformer oil degradation (acid value >0.1mg KOH/g)
- Moisture contamination (>30ppm)
- Solid insulation carbonization
Prevention:
✅ Oil testing every 6 months (DGA for H₂, C₂H₂ gases)
✅ Use vacuum oil purifiers (keep moisture <15ppm)
✅ Select high-stability oil (KI≥55) for replacements
2. Oil Leakage Issues (25% of Cases)
Common Leak Points:
- Gasket seals (hardens in 3-5 years)
- Valve flanges
- Radiator weld seams
Solutions:
🔧 Install fluororubber gaskets (-40℃~200℃ resistant)
🔧 Use torque wrenches (bolt pressure ≤35N·m)
🔧 UV fluorescent dye testing (detects 0.1mm cracks)
3. Overheating Risks (15% of Cases)
Cause | Critical Temp | Solution |
---|---|---|
Overloading | >105℃ | Install fiber-optic sensors |
Cooling system clog | ΔT oil >25K | Monthly radiator cleaning |
Tap changer contact wear | Local >130℃ | Use vacuum OLTC |
4. Electrical Faults (10% of Cases)
Critical Issues:
- Winding short circuits (partial discharge >10pC)
- Bushing flashover (insufficient creepage)
- Core ground faults (>100mA current)
Prevention:
⚠️ Annual FRA winding tests
⚠️ Silicone composite bushings (anti-pollution)
⚠️ Core ground current monitors
5. Emergency Failures (5% of Cases)
- False gas relay trips → Install oil flow relays
- Pressure relief valve sprays → Use dual-piston valves (<70kPa)
Maintenance Gold Standards
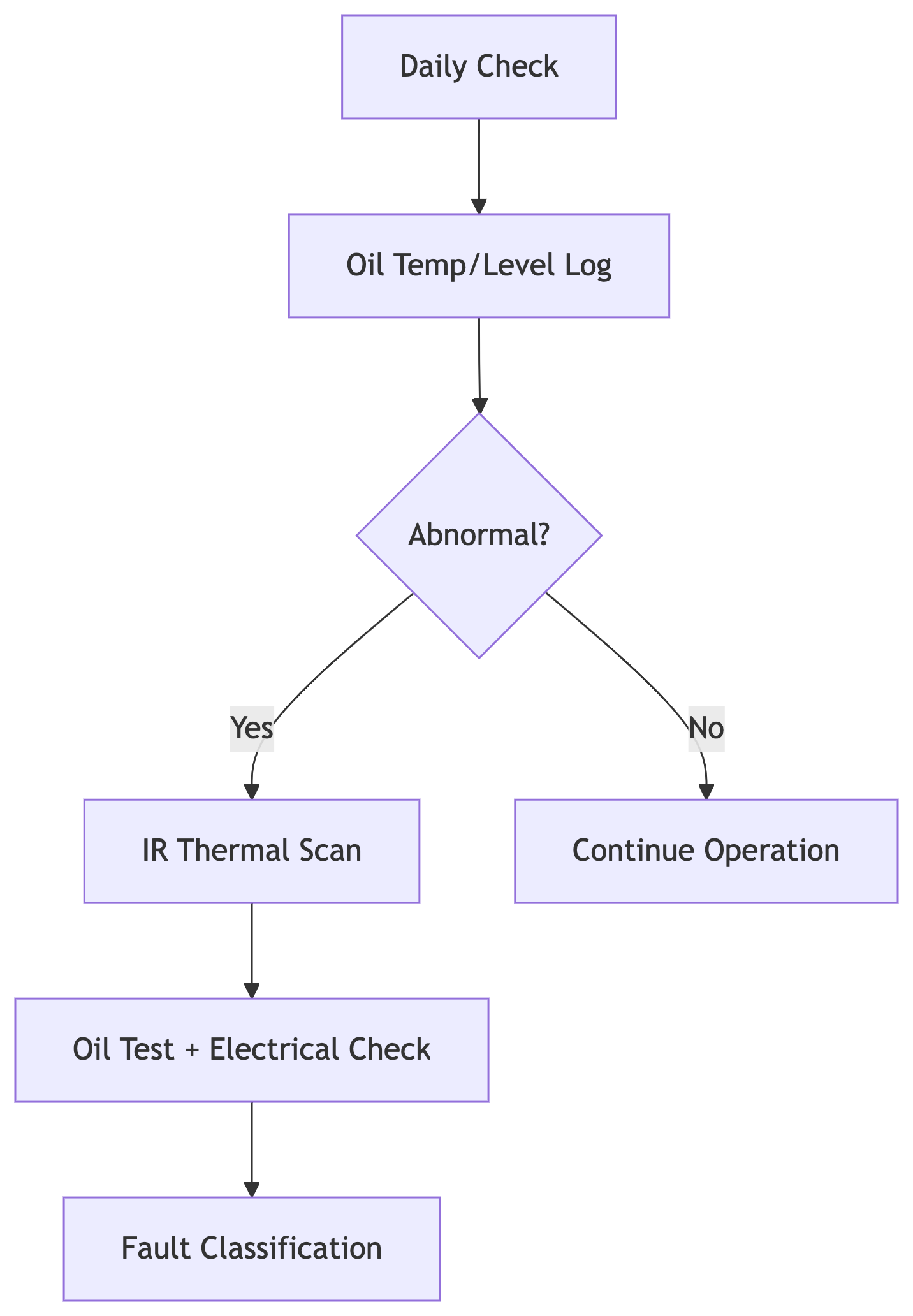
Must-Have Tools:
- FLIR T540 thermal camera
- Kelman Transfix oil analyzer
- UE Ultraprobe ultrasonic detecto
3 Key Life-Extension Tips
- Load Management: Keep 65-80% loading
- Oil Reconditioning: Add adsorption degassers (2-3x oil life)
- Corrosion Protection: Apply polyurethane tank coating