Traditional analyses of distribution transformers have predominantly focused on technical parameters and operational performance, often overlooking their comprehensive value throughout the entire life cycle. This article explores the holistic impact of distribution transformers—from raw material extraction to decommissioning and recycling—through three key dimensions: economic costs, environmental footprint, and social benefits. This perspective aims to provide new insights for the sustainable development of the power industry.
1. Life Cycle Cost Analysis (LCCA)
1.1 Initial Investment Cost Breakdown
- Material Costs (60-70% of total):
Silicon steel sheets (~35%), copper (25%), insulation materials (15%)
Case example: Copper-wound 1000kVA oil-filled transformers cost ~20% more than aluminum-wound equivalents - Manufacturing Costs:
Amorphous alloy transformers cost 30-40% more than traditional silicon steel transformers - Transportation & Installation Costs:
Mountainous area projects may incur 3x higher transport fees compared to flat terrains
1.2 Operational Cost Model
Cost Type | Share | Key Influencing Factors |
---|---|---|
No-load losses | 40% | Core material, design technology |
Load losses | 35% | Winding resistance, cooling efficiency |
Maintenance | 15% | Insulation aging, environmental corrosion |
Failure losses | 10% | Reliability design, monitoring systems |
1.3 Decommissioning Costs
- Oil-immersed transformers:
Waste oil disposal costs ~¥2000/ton (including PCB testing) - Copper recycling value:
Current market prices recover ~60% of original copper material costs
2. Carbon Footprint Tracking (LCA-Based)
2.1 Carbon Emission Intensity by Phase
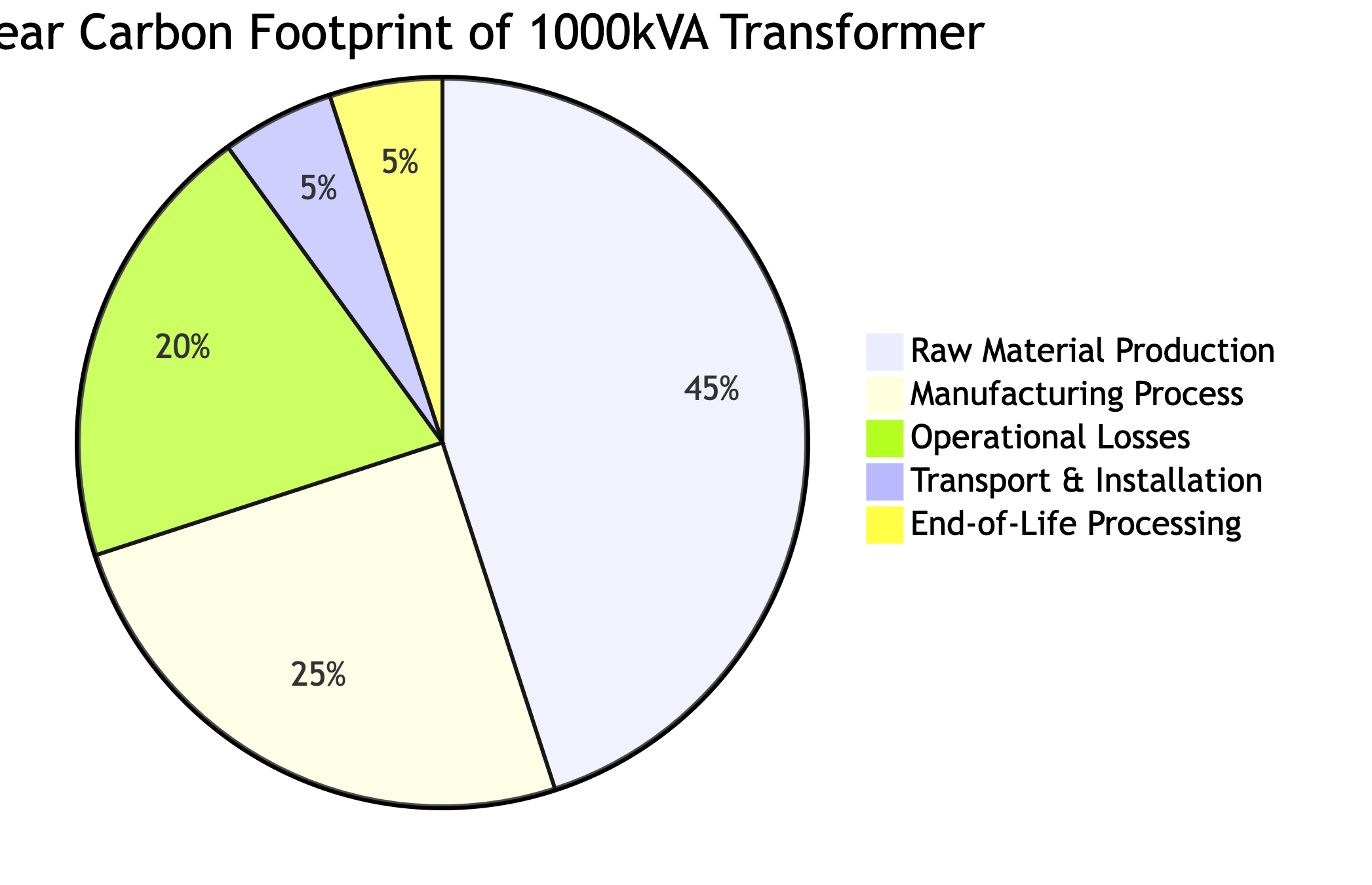
2.2 Key Decarbonization Levers
- Material Substitution:
Amorphous alloy transformers reduce lifecycle emissions by 18% - Efficiency Improvements:
Tier-1 efficiency transformers cut operational emissions by 12% vs. Tier-3 - Lifespan Extension:
Extending service life from 20 to 30 years decreases annualized carbon emissions by 22%
3. Circular Economy Practices
3.1 Innovative Recycling Technologies
- Oil sludge pyrolysis:
Enables 90% mineral oil regeneration - Epoxy resin decomposition:
ABB Switzerland developed low-temperature catalytic decomposition technology - Silicon steel reprocessing:
Kawasaki Heavy Industries achieves <5% loss rate with laser cutting reuse
3.2 Business Model Innovations
- Transformer-as-a-Service (TaaS):
Siemens pilots kWh-based leasing models - Shared Backup Capacity:
Dutch utility Enexis establishes regional transformer sharing pools - Residual Value Insurance:
Tokio Marine offers end-of-life value guarantee products
4. Policy & Standard Developments
4.1 Global Regulatory Trends
- EU’s 2024 Ecodesign Regulation for Transformers:
Mandates full lifecycle environmental data disclosure - US EPA New Rules:
Requires PCB content <50ppm starting 2025 - China’s “Dual Carbon” Targets:
State Grid mandates carbon footprint-certified transformers for new projects
4.2 Certification Systems Evolution
- IEC developing:
Guidelines for Transformer Environmental Performance Evaluation - Third-party certifications emerging:
Environmental Product Declaration (EPD)
Cradle to Cradle Certified™
Conclusions & Recommendations
- Procurement Strategy Shift:
Transition from “lowest bid” to “lowest lifecycle cost” evaluation - Technology Innovation Priorities:
Develop modular designs for easier disassembly and recycling - Policy Recommendations:
Establish transformer carbon footprint databases and trading mechanisms
With growing ESG adoption, distribution transformers are evolving from mere electrical equipment into embodiments of corporate sustainability commitments. Within five years, “green transformers” featuring traceable materials, modular repairable designs, and digital carbon management will become the market mainstream.